What is pressure sensitive adhesive?
Pressure sensitive adhesive is mainly acrylic and rubber series of solvent or latex adhesives. Due to the need for high-speed operation, reasonable coating, and elimination of solvent pollution problems, the development of warm melt pressure sensitive adhesive, hot melt adhesive, and pressure sensitive adhesive characteristics in one, no solvent, no pollution, and easy to use. It is applied in a molten state, cooling, and curing after applying mild pressure to the adhesive effect.
It has high peeling power. It is suitable for the adhesion of pressure sensitive tape, labels, BOPP, double-sided tape, paper cloth, and other materials with high stripping force. It can also be used for bonding all kinds of plastic paper and pasting nameplates and trademarks on all kinds of materials.
- High peeling strength, good initial adhesion, and retention
- Excellent compatibility with all kinds of color master
- Excellent transparency
- Excellent stripping performance, strong cohesion of the film
- Water-based emulsion, non-toxic and non-combustible,
- Single component, easy to use
- Fast drying speed
- Good aging resistance
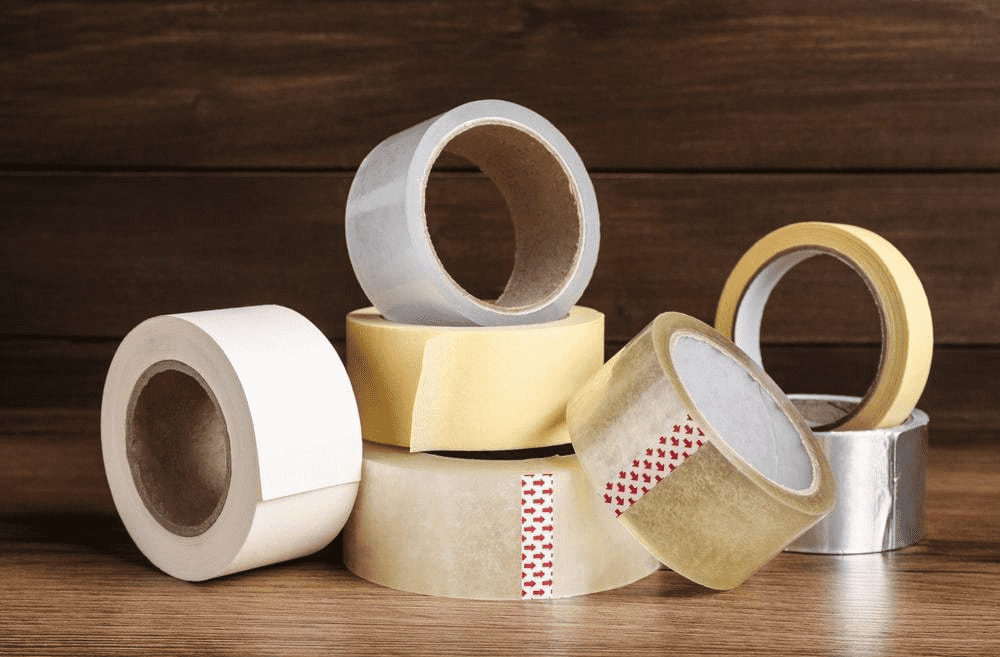
Use of pressure sensitive adhesive
Pressure sensitive adhesive has a wide range of applications, which can be used in diapers, women’s products, double-sided tape, labels, packaging, medical and health care, bookbinding, surface protective film, wood processing, wallpaper, and shoe making. Among them, the consumption of HMPSA for packaging is large, accounting for almost half of the total.
The main component of hot melt pressure sensitive adhesive is styrene thermoplastic elastomer. Hot melt pressure sensitive adhesive has the advantage of no solvent, so no air pollution, and high productivity. But the disadvantage is heat resistance, and lack of cohesion. New thermoplastic elastomers such as SEBS, SEPS, and epoxidized SBS are used to prepare warm melt pressure-sensitive adhesives with higher properties.
New acrylic ester block copolymer heat resistance, oxidation stability, UV stability, and good adhesion to HDPE, stainless steel, glass, polystyrene, acrylic plate, polycarbonate, nylon, polypropylene, and other materials, can be used to make the medical tape, transparent film, labels, etc. Acrylic polymer combined with a water-soluble polymer to produce hot melt pressure sensitive adhesive with water dispersion. Acrylic polymer disperses into non-adhesive particles below 100μm in weak alkali aqueous solution, which is easy to separate and suitable for recycling old paper. Acrylic copolymers with low Tg were obtained by copolymerization of acrylate monomers containing the benzophenone group.
Warm melt pressure sensitive adhesive, UV irradiation easy crosslinking, the advantage is that there is no need to add photoinitiator, no initiator residue problem.
Can be low temperature (120~140℃) warm melting coating, low VOC, low odor, no skin irritation, and good thermal stability. The composition of pressure sensitive adhesive tape is a special type of adhesive, that is, the adhesive liquid is coated on the substrate and processed into a strip, and made into a coiled supply, including solvent-activated adhesive tape, heating adhesive tape, and pressure sensitive adhesive tape. The composition of pressure sensitive adhesive tape: ① pressure sensitive adhesive ② substrate ③ bottom treatment agent ④ back treatment agent ⑤ The main components of isolation paper pressure sensitive adhesive include rubber type and resin type.
Such as polyacrylate or polyvinyl ether two classes, the substrate requires a uniform, small scalability and good solvent infiltration, including:
- Fabrics such as cotton, glass, or non-woven fabrics.
- Plastic films, such as PE, PP, PVC, and mylar film.
- Paper such as kraft paper, transparent glass paper, etc.
The substrate roughness is between 0.1 and 0.5. The role of the underlying treatment agent is to increase the adhesive strength between the adhesive and the substrate so that the adhesive tape will not cause the adhesive and the substrate to disengage and stain the adhesive surface and make the adhesive tape reuse.
The common base treatment agent is chloroprene rubber, modified chlorinated rubber, partially vulcanized with isocyanate. The back primer is generally prepared from polyacrylate, PVC, cellulose derivatives, or organosilicon compounds. It can act as an isolation agent. Double-sided adhesive tape should be added with a layer of isolation paper such as semi-hard PVC film, PP film, or kraft paper. The pressure-sensitive adhesive does not need to warm, can be bonded with finger pressure, and is a peel-strength adhesive, its adhesion characteristics are four elements: T (fast adhesion) adhesive layer cohesion strength; K- adhesive base force is the adhesive force between the adhesive and the substrate.
Wuxi Changsheng Adhesive Products Co., LTD., the company specializes in R & D, production, and sales of pressure sensitive adhesive series products, if you need to consult, you are welcome to inquire or Email.