Do you know about pressure-sensitive adhesives? Pressure-sensitive adhesive is an adhesive kind featuring a special formulation. It binds together two surfaces upon applying pressure and does not need water, solvent, or heat activation. The advantage of pressure-sensitive adhesive is it is waterproof and odorless.
Pressure-sensitive adhesive combines viscosity with elasticity. Viscosity refers to the thick state, that is semi-fluid and sticky in consistency. It is the same as honey. Elasticity is stiff and solid, like rubber. It adheres well on a surface, consisting of adhesive substances in the raw materials.
The pressure-sensitive adhesives are not actual solids. It means with the increase in temperature, the bond, and the strength decrease. This adhesive type is permanently sticky and strong at room temperature.
What is the difference in pressure-sensitive adhesives?
The pressure-sensitive adhesive does not need much pressure, while other types require solvent, water, or heat to work as the adhesive. Engineers find pressure-sensitive adhesives useful due to the properties of load-bearing. It means the bond is strong to bear the required weight.
Pressure-sensitive adhesive tapes are known as PSA. They are self-stick adhesive, self-adhesive, featuring viscoelasticity. It is a polymer with this feature, viscoelasticity and which means the material is solid and liquid. The tape stays sticky on peeling and protects the adhesive. The demand for PSA is growing as this tape is simple to use, and is a cost-effective fastening solution.
The adhesive system repeatedly is useful for reuse. The strength of the adhesive stays the same with each cycle of adhesion, and reversing adhesion is a fast process, relatively.
Pressure-sensitive adhesive (PSA) tape characteristics
PSA tape features three qualities, such as:
- Cohesion- It is the adhesive strength or the stickiness strength.
- Adhesion– It is the adhesive strength, where the sticky material or the surface tape sticks to the substrate.
- Tack– It is the adhesive time taking to any surface or substrate. Any the sticks with little pressure, while a less tacky tape requires harder pressure to stay in sticking.
A tape is a pressure-sensitive adhesive when it bonds with pressure. Any tape involving heat or a solvent is not a pressure-sensitive adhesive tape.
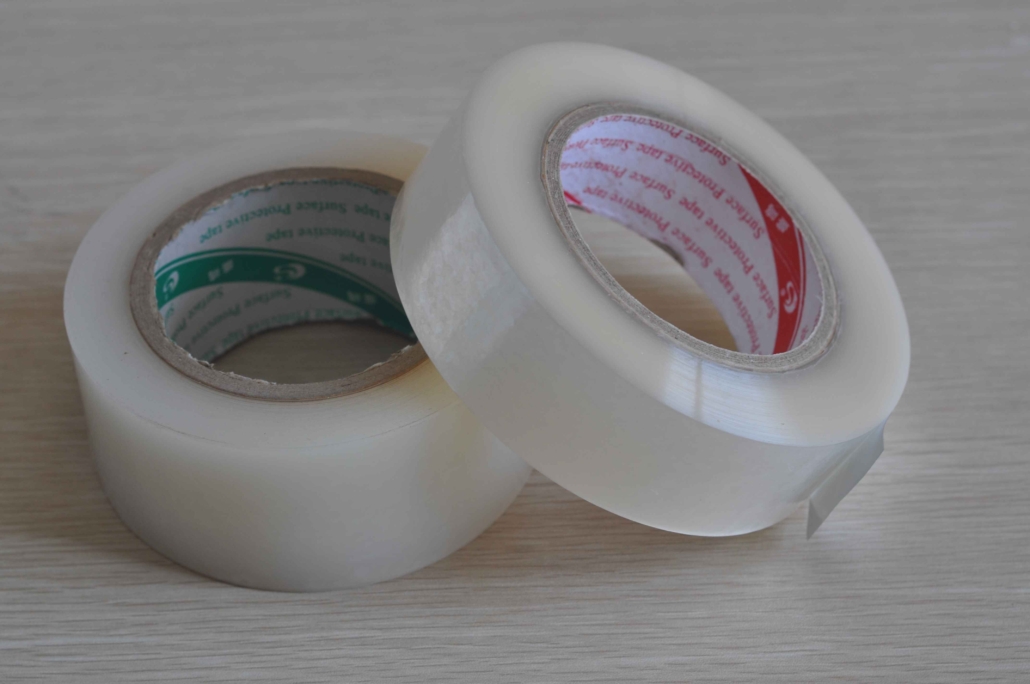
Benefits of using Pressure-Sensitive tape
Pressure-sensitive tape is an efficient and quick tape. It is gaining popularity for various reasons:
- The material of PSA tapes is light and thin, making working easy with them.
- Fast to bond, so requires no other element to activate, but for pressure. It bonds dissimilar materials, so no worries about the compatibility of materials.
- The PSA tapes reduce the noise of vibrations. The tapes absorb noise and do not rattle like any traditional fastener.
- PSA reduces refinishing a surface need and eliminates visible mechanical fasteners. There is no fastener or screw, but there is a smooth finish.
- PSA tapes fill gaps, creating uniform thickness and creating aesthetically pleasing products.
What Adhesive types are used for PSA tapes?
Rubber: The rubber-based adhesives are synthetic or natural rubbers. They are formulated with oils, resins, and anti-oxidants. It is a cost-effective PSA, offering quick sticking ability, but not an appropriate choice for high-heat applications.
The rubber-based PSA are easily removable and suitable as a permanent bonding option. They are designed to optimize PSA applications, and they are popular for their reliability, quality, and efficiency. They are ideal for manufacturing industries or organizations dealing with:
- Packing list envelopes, Food labels, Specialty labels, Tire and Fabric labels, Permanent General purpose labels, and Resealable and Removable labels.
Acrylic: Acrylic-based adhesives are pressure-sensitive adhesives featuring acrylic polymers. They feature long-term aging and have resistance to environmental factors and solvents. These adhesives develop a stronger bond and manage higher temperatures.
The acrylic PSAs are versatile and offer better UV stability, provide lower operating temperatures, and improve clarity. The applications withstand temperature and moisture changes in the application. These adhesives provide advanced bonding as they are coater-ready. They are ideal for industries dealing with:
- Pharmaceutical labels, Clear labels, Foam tape, Resaleable, and Removable labels, General purpose permanent labels, and Mounting tape.
The graphics industry also relies on the emulsion-acrylic PSAs for their clean removability, high clarity, and cohesion, making them ideal for various purposes including:
- Corporate and architectural graphics
- Exhibition graphics
- Removable protective film
- Advertising graphics
Precisely, the emulsion-acrylic PSAs are useful in medical product manufacturing. They are skin safe and suitable for:
- Bandages, Wound dressings, and Medical tape
Another vital market using emulsion-acrylic PSAs is food contact. They are 100% safe as food-based applications. It is tested and tried to receive food range approval. These adhesives offer good adhesion and reliability, being consumer safe.
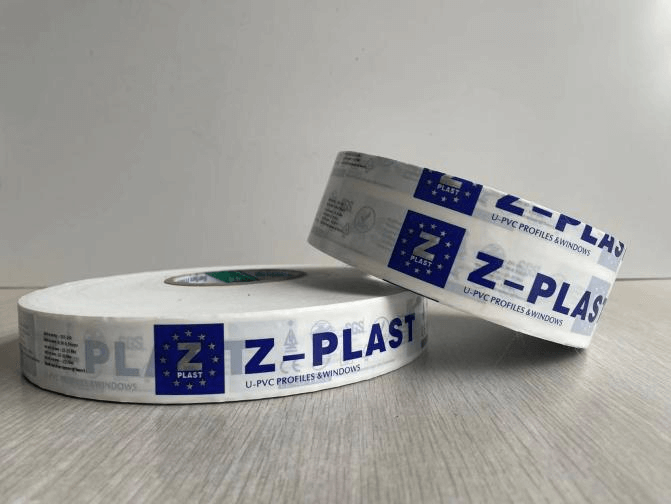
Silicone: The silicone polymer’s formulation and the adhesive bonds with silicon substrates. These adhesives of silicone are expensive and have a low initial tack. Yet, they withstand higher temperatures in comparison to acrylic and rubber adhesive.
Solvent acrylic PSAs assure the product’s resistance to weathering, moisture, UV, and a few chemicals, besides operating temperature. Manufacturers opt for solvent-based PSA for production, owing to its durability and strength that manages under challenging conditions. It is resistant to chemical and weather exposure, and UV, and is suitable as PSAs for a variety of applications:
- Automotive tape
- Exhibition graphics
- Pharmaceutical labels
- Over-laminating films
- Durable labels
- Ostomy care
- Vehicle graphics
- Conspicuity tape
- Resealable and Removable labels
- Surgical drapes
- Would dressings
These PSAs withstand chemical contact and extreme temperatures that fulfill the need for supporting applications. Manufacturers require adhesive to various substrates to safeguard customers in extreme conditions. The pressure-sensitive adhesives are useful for pipe marking appliances to drum labels and work under extreme conditions perfectly as strong bonds.
UV-curable PSAs offer the freedom to get more options and grab the consumer’s attention. These PSAs optimize productivity for thicker tapes. PSAs are offering superior clarity and offer no-look labels featuring 100% coating benefits as solids technology. As per silicone material, the material lasts ranging from 6 to 12 months. It features a release liner or comes with a self-wound.