“Environmental protection, health, safety” is a global topic, but also the focus of the industry. The flexible packaging industry is no exception, especially in recent years, the rapid growth of the flexible packaging industry and the wide application of flexible packaging, the impact on the environment, health, and safety problems are increasingly prominent, among them, flexible packaging compound adhesive has been one of the core issues discussed. At present, countries all over the world are actively exploring the alternative products of two-component solvent-based polyurethane adhesives, such as solvent-free adhesives, hot melt adhesives, water-based polyurethane adhesives, alcohol-soluble polyurethane adhesives, and other environmental adhesives, and has made great progress in some fields.
Environmental protection adhesive research and development and marketing, countries have taken a very different way, take different measures. In Europe, the research of water-dispersed polyurethane adhesives and solvent-free adhesives has been at the forefront, and its market development is fast. In the United States, reactive hot-melt adhesives have developed rapidly, but no new adhesives can completely replace solvent-based two-component polyurethane adhesives. Moreover, from the overall situation of the current market, the demand for solvent-based polyurethane adhesives is still growing, and the growth amount is far more than other types of adhesives.
1. Water-based
The water-based adhesive is prepared water-based adhesive with water as a solvent or dispersing medium. Because of the absence of organic solvent, solvent pollution is eliminated. It should be pointed out that not all water-based adhesives are pollution-free, such as urea-formaldehyde glue and 107 glue are water-based glue, but pollution is very serious. Emulsion acrylate pressure-sensitive adhesive can replace solvent-based pressure-sensitive adhesive. Water-based refilm adhesive has begun to replace solvent-based refilm adhesive, non-toxic, non-combustion, pollution-free, and safe to use. A new type of water-based polyurethane adhesive has been developed in Japan, which is suitable for automobile interior decoration and may replace the current common solvent adhesive. In polyvinyl alcohol (PVA) aqueous solution with isocyanate or prepolymer, vinyl polyurethane emulsion, can replace the urea aldehyde glue, and completely solve the problem of formaldehyde release. Water-based adhesives are favored for their non-toxicity and non-pollution, but their shortcomings are slow drying speed, poor water resistance, and poor frost resistance. The solid part should be increased, the drying speed should be accelerated, and the cross-linking method should be adopted to improve the drying speed and water resistance, so as to expand its application.
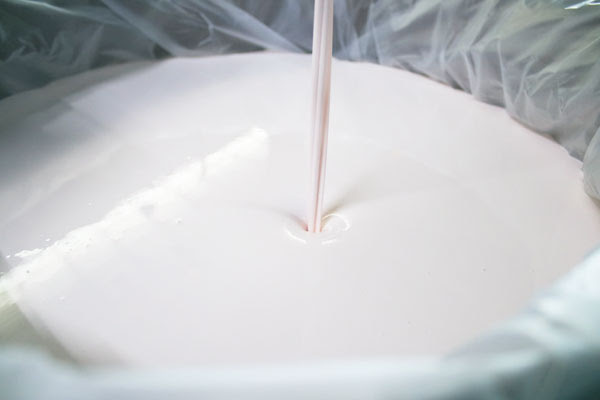
2. No solvation
Solvent-free refers to an adhesive that does not contain solvent, because no solvent in the atmosphere volatilized, will not cause pollution and harm. The vast majority of epoxy adhesives, anaerobic adhesives, cyanoacrylate adhesives, aerobic modified acrylate structural adhesives, solvent-free polyurethane adhesives, and photocuring adhesives are solvent-free varieties.
3. Solidization
Solid is the adhesive used in solid forms, such as hot melt glue, hot melt pressure sensitive glue, water-soluble powder glue, reaction type stick glue, and office solid glue stick, with no volatiles released in the coating and bonding process, completely no environmental pollution. Foreign countries recommend the use of powder adhesive with stable performance, no environmental pollution, and other advantages. American CP adhesive company produced a urea-formaldehyde tree fat powder, that contains a curing agent and filler, no smell, no pollution, and no poison, used as an excellent universal wood adhesive. In China, there has been a new type of high-strength and high-quality powder adhesive — Bangjia strong adhesive powder, mixed with water to become a polymer dispersion, with outstanding adhesion, water resistance, and aging resistance. The United States produced an epoxy glue stick for emergency repair, plugging very conveniently.
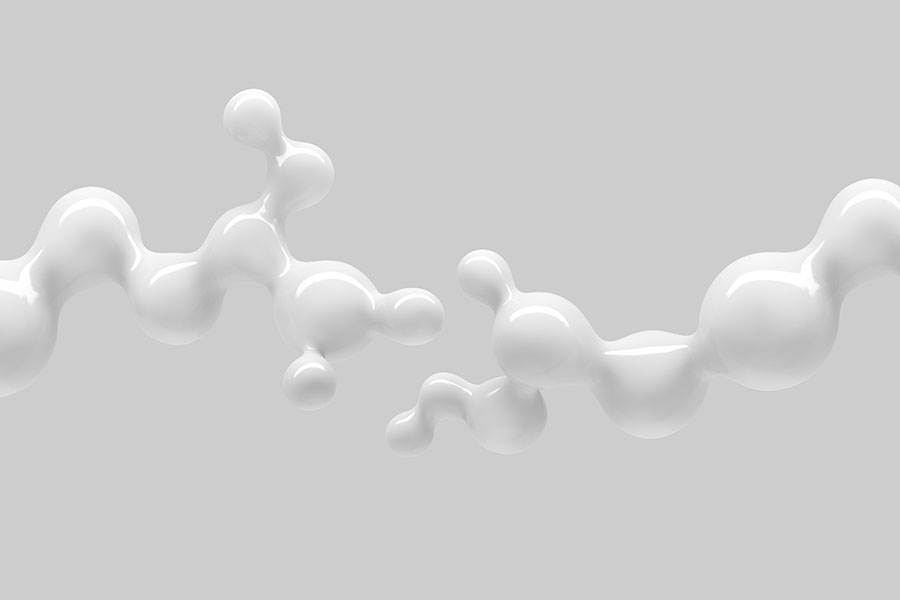
4. Solvent-based adhesives use low-toxic and non-toxic solvents
Solvent-based adhesives have fast drying speed and good water resistance. Although they are polluted and toxic, they cannot be completely replaced by water-based adhesives at present. Non-toxic or non-toxic solvents can be used, such as cyclohexane, ethyl acetate, dimethyl carbonate, etc., to make non-toxic or low-toxic solvent-based adhesives. The domestic market has appeared in shoes with no “triphenyl” polyurethane adhesive, grafting chloroprene adhesive, and SBS-type special effects all-purpose adhesive. Dimethyl carbonate (DMC) is a new and good solvent with low toxicity. DMC has been used as the main solvent for the preparation of solvent-based adhesives in Japan, and large-scale production has been formed in China.
The new cleaner production technology can realize the unity of economic benefit and environmental benefit and produce environment-friendly adhesive. Ditch the smelly methyl methacrylate in favor of a higher boiling point monomer. Production of modified acrylate fast-setting structural adhesive. In the adhesive preparation and production process do not use toxic raw materials, such as formaldehyde, chlorinated solvent, aromatic solvent, containing a toxic heavy metal filler, etc. In non-toxic and harmless conditions for production, such as using polyformaldehyde instead of formaldehyde solution to produce a modified amine curing agent. By increasing the dosage of hydrochloric acid and reducing pH, the reaction of polyvinyl formaldehyde can be more complete, the content of free formaldehyde can be reduced to less than 0.2%, and the smell of formaldehyde can not be heard basically. Adding formaldehyde catcher, such as starch, polyvinyl alcohol, melamine, etc., can significantly reduce the content of free formaldehyde in urea-formaldehyde resin adhesives. Among them, oxidized starch had a better effect than ordinary starch, and the content of free formaldehyde was less than 0.1%.