Pressure sensitive adhesive, is a slightly applied pressure can be an instantaneous adhesive. Pressure sensitive adhesive is a kind of adhesive for manufacturing adhesive tape, divided into solvent activation type, heating type and pressure sensitive type three types, the pressure sensitive type of the use of the most convenient, rapid development.
Classification of pressure sensitive adhesives
Pressure sensitive adhesive can be divided into rubber type pressure sensitive adhesive and resin type pressure sensitive adhesive according to the type of adhesive. Rubber type pressure sensitive adhesive is composed of rubber as adhesive, adding viscosifier, filler and antioxidant. According to the types of rubber, it can be divided into natural rubber, polyisobutene rubber, styrene butadiene rubber pressure sensitive rubber and so on. The adhesive of resin pressure sensitive adhesive is synthetic resin, including homopolymer resin and copolymer resin. When preparing pressure sensitive adhesive, it is necessary to add thickening agent, softener, filler and antioxidant. According to the type of resin, it can be divided into polyolefin, chloro-vinegar copolymer, acrylic resin, silicone and fluorine resin pressure sensitive adhesive.
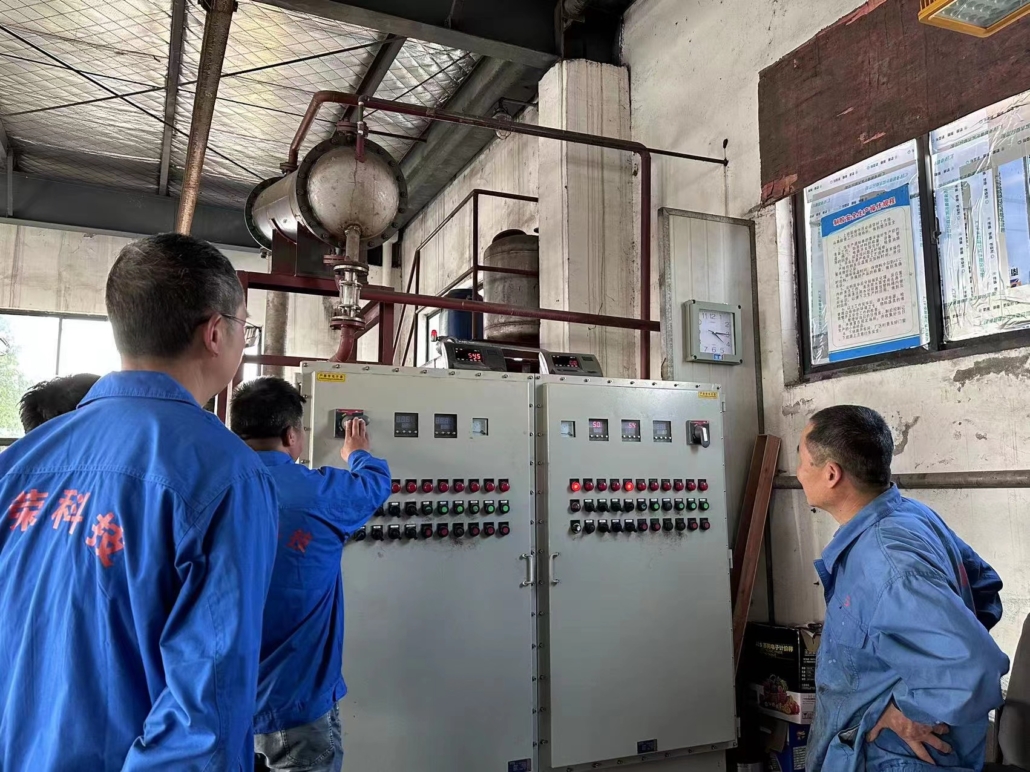
Composition of pressure sensitive adhesive
In addition to the adhesive, the pressure sensitive adhesive should be added to the adhesive and other auxiliary substances.
- Adhesive pressure sensitive adhesive has rubber or synthetic resin and other materials, its role is to give the adhesive layer sufficient cohesion strength and bonding, the amount of 30%-50%.
- Viscosifier. Viscosifiers are rosin and its derivatives, petroleum resin, etc., whose function is to increase adhesive adhesion. Its use is 20%-40%.
- Plasticizer. The plasticizer used for general plastic processing, its role is to increase the fast viscosity of the adhesive layer. The amount used is 0-10%.
- Antioxidant. General rubber, plastic antioxidant can be used, the role is to improve the service life, the dosage is 0-2%.
- Stuffing. The filler used is the general plastic filler, the function is to improve the cohesion strength of the adhesive layer, reduce the cost, the dosage is 0-40%. In addition, for some pressure sensitive adhesives, also need to add viscosity regulator, vulcanizing agent and solvent.
Commonly used pressure sensitive adhesive
At present, the commonly used pressure sensitive adhesives mainly include rubber pressure sensitive adhesive, acrylic pressure sensitive adhesive and silicone pressure sensitive adhesive three types.
Rubber pressure sensitive adhesive. Rubber pressure sensitive adhesive is the most widely used kind of pressure sensitive adhesive, the rubber used is natural rubber, synthetic rubber and recycled rubber. The natural rubber as adhesive has good compatibility, pressure sensitivity and creep resistance, poor aging resistance, and great hardness change. The pressure sensitive adhesive made of synthetic rubber has better heat resistance and durability than that of natural rubber, but the bonding strength is worse. Using recycled rubber as adhesive can only use the recycled rubber of natural rubber, the recycled rubber of synthetic rubber effect is very poor, should not be used. For the pressure sensitive adhesive with natural rubber as adhesive, natural rubber can be used with synthetic rubber, partial vulcanization crosslinking, grafting modification or adding appropriate reinforcing filler modification. These methods can improve the aging resistance of the adhesive layer and prolong the service life of the adhesive.
Acrylic pressure sensitive adhesive. Acrylate pressure sensitive adhesive is second only to rubber type pressure sensitive adhesive at present, its adhesive is the copolymer of acrylate and other ethylene monomers. Copolymeric monomers can be divided into primary monomer, secondary monomer and functional monomer. The main monomer has butyl acrylate, etc., which provides toughness and adhesiveness. The secondary monomers include methyl methacrylate, styrene, etc., which are hard monomers and can provide rigidity and cohesion strength.
Functional monomers are monomers containing other functional groups, such as hydroxyethyl methacrylate, etc., which can play a cross-linking role in the polymerization process, further improving the adhesion, cohesion and heat resistance creep. This scientific monomer combination can make the copolymer itself have the basic properties of pressure sensitive adhesive, so the acrylic pressure sensitive adhesive is almost one component. Compared with rubber type pressure sensitive adhesive, acrylic type pressure sensitive adhesive without antioxidant has excellent weather and heat resistance, good oil resistance, adhesive layer transparent and no phase separation and migration phenomenon. Due to the introduction of various polar groups through copolymerization, which increases the secondary force effect between molecules, it has relatively large bonding strength and cohesion strength.
Silicone pressure sensitive adhesive. Silicone pressure sensitive adhesive is made of silicone rubber and silicone resin. Silicone rubber is the basic component of pressure sensitive adhesive and silicone resin is the viscosifier. The properties of pressure sensitive adhesive vary with the ratio of the two. In the formulation, the relative molecular weight of silicone gum is about 1.5×10, but for the appropriate selection of silicone resin, an active end group is required at the end. Commonly used are methyl silicone resin, methyl phenyl silicone resin, phenyl vinyl silicone resin. They have good thermal stability, silicone pressure sensitive adhesive bonding performance is good, bonded on aluminum sheet, the strength is 21MPa, after 260℃, 7 days, the strength remains unchanged, as the backing material of silicone pressure sensitive adhesive polyester, polyester, etc.
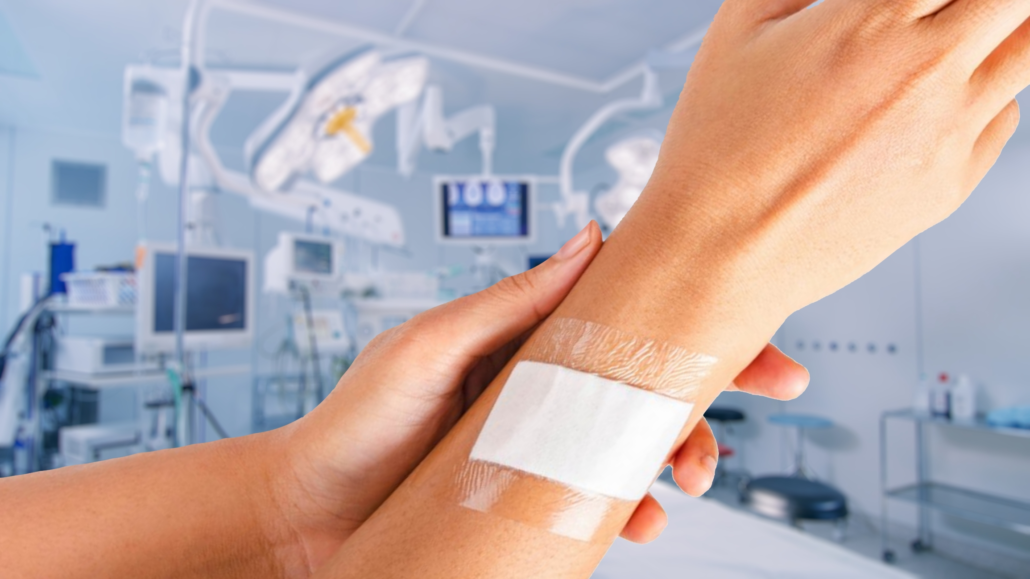
The composition of pressure sensitive adhesive tape:
The pressure sensitive adhesive tape is generally made into a ribbon reel, which has three forms of single-side adhesive coating, double-side adhesive coating and adhesive sheet. Single side coating is in the front of the substrate coated with the base coating agent and then coated with pressure sensitive adhesive, the reverse side coated with the back treatment agent can be rolled. Double-sided adhesive tape and single-sided adhesive film do not need a back primer, but need a layer of isolation paper on a adhesive surface. The base material of adhesive tape is the basic material of pressure sensitive adhesive. As the base material of pressure sensitive adhesive, it must have good mechanical strength, uniform thickness, not easy to deformation, and good wetting with pressure sensitive adhesive. Commonly used substrates are cotton, glass cloth, synthetic fibers and other fabrics, polyethylene, polyester, polyvinyl chloride and other plastic films.
Bottom coating agent, also known as bottom treatment agent, bottom glue. The base coating agent is coated between the pressure sensitive adhesive and the substrate can enhance the adhesion of the pressure sensitive adhesive to the substrate and prevent degumming. There are two types of base coating: combination type and grafting type. Mixed base coating is a mixture formed by blending a resin that has affinity for the substrate and a resin that has affinity for the pressure sensitive adhesive. The graft copolymerization base coat is based on the resin chain with affinity for pressure sensitive adhesive, and the monomer of the resin with affinity for the substrate is grafted copolymerization. Some pressure sensitive adhesive and strong adhesion between the substrate can not be coated with primer.
The so-called back primer is a layer coated on the back of the single-sided adhesive tape substrate that acts as an interlayer isolation when the adhesive tape is rolled into a circle. The primer also improves the physico-mechanical properties of the substrate. It is required to have good interlayer isolation ability when selecting the back treatment agent. It is also required to have good transparency and non-mobility when peeling off the tape. Commonly used back primer are polyacrylate, polyvinyl chloride, cellulose derivatives and organosilicone compounds. Different substrate or pressure sensitive adhesive, the selection of different primer, can also be used in combination with several primer.
For double-sided adhesive tape, label, adhesive paper, adhesive sheet, etc., the pressure sensitive adhesive surface should be covered with a layer of isolation paper. The commonly used isolation paper is semi-rigid polyvinyl chloride film, polypropylene film and coated with back primer kraft paper.
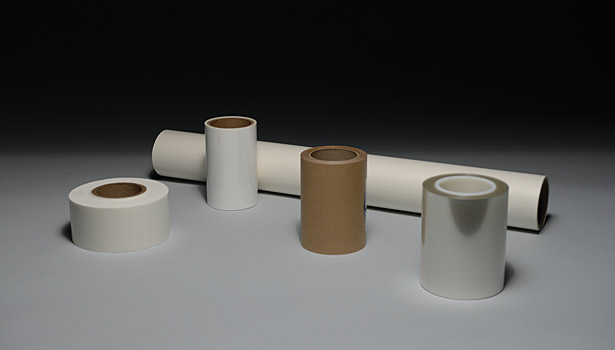
The adhesion characteristics of pressure sensitive adhesive:
The pressure sensitivity of pressure sensitive adhesive is the performance of its adhesion characteristics, which are composed of four elements: fast adhesion (A), adhesion (B), cohesion (C) and adhesion force (D). Fast adhesion (A) refers to an interface peeling force manifested when the adhesive tape and the adhesive are separated immediately after contact with the lightest pressure and the fastest speed. It can be understood as the initial viscosity, showing the viscosity and the ability of pressure sensitive adhesive to infiltrate the adhesive, so it is difficult to make a strict definition. Adhesion (B) refers to the peeling force between the adhesive tape and the adhesive surface after proper pasting, and its size determines the adhesive property of the adhesive tape. Cohesion (C) is the cohesive strength of the adhesive layer, which is related to the intermolecular force, intermolecular bond, molecular size and intermolecular arrangement. The adhesive base force (D) is the adhesive between the pressure sensitive adhesive and the substrate or the adhesive between the pressure sensitive adhesive and the substrate and the substrate. Because these four forces have to satisfy.
Preparation process of pressure-sensitive adhesive tape:
The preparation technology of pressure sensitive adhesive tape often adopts different technology and equipment because of different substrate, adhesive type, type of film and shape of adhesive tape.
Prepare pressure sensitive adhesive. The pressure-sensitive adhesive suitable for solvent coating is firstly dissolved in solvent, then added with other components, stirred well, and prepared into a adhesive liquid with certain viscosity for reserve. If the adhesive is rubber, it is best to conduct plain refining first in order to increase the quick adhesion and solubility, and appropriately reduce cohesion. It is suitable for the pressure sensitive adhesive coated by the rolling method. Generally, it is mixed evenly on the rubber machine according to the order of rubber, antioxidant, resin (viscosifier), plasticizer, viscosity regulator and filler, and then a small amount of solvent is added to dilute to a certain viscosity.
Pressure sensitive adhesive coating. After the pressure sensitive adhesive, base coating agent and back treatment agent are prepared, they can be coated on the substrate by solvent method or rolling method and then the solvent is removed. The thickness of the adhesive layer is appropriate to be 0.02-0.03mm. When the solvent method is applied, the base coating agent and the back treatment agent are first coated on two different surfaces of the base material in the process of the progress of the base material, and then the pressure sensitive adhesive is coated after drying. The whole process is continuous. Solvent method equipment is simple, easy to operate, a wide range of coating thickness, especially suitable for coating on the substrate with low strength. The disadvantage is that a large amount of solvent is consumed, which increases the cost and pollutes the environment.
Rolling method sizing sequence and solvent method is basically the same, but try to distribute the glue liquid on the roll, so that the substrate to be coated in two rollers (one or both coated with glue) through to complete the coating, the thickness of the rubber can be adjusted between the distance between the two rollers. The rolling coating method does not use or less solvent, the cost is low, the pollution is small, the thickness of the adhesive layer is uniform, the construction is safe and convenient, but the equipment is more complex, only the adhesive should be coated on the substrate with higher strength. Improved rolling methods, such as isolation rolling, have a wider application and can be used to apply glue to any substrate.

The application of pressure sensitive adhesive in electronic and electrical appliances:
Pressure sensitive adhesives are widely used in electronic and electrical appliances, mainly reflected in the following aspects.
Electrical insulation. Electrical insulation is mainly transformer, electromagnetic coil winding insulation and insulation between layers, wire and cable connector and end insulation. The most commonly used are PVC tape and polyester tape. When heat resistance is required, silicone pressure sensitive adhesive can be used, and tape based on glass cloth, polytetrafluoroethylene or polyimide. Small transformer and low voltage coil with PVC, polyester, polypropylene or impregnated, coated paper and cloth and other substrate pressure sensitive tape as winding insulation, end fixation and sealing. Aromatic polyamide and glass tape should be used for large transformers requiring heat resistance. Polyimide, polytetrafluoroethylene or silicone impregnated glass tape can also be used. In order to improve the electrical insulation performance of the transformer, vacuum impregnation of insulating paint is generally carried out. At this time, the pressure-sensitive tape should be resistant to impregnation of insulating paint.
Welding masking and surface protection. The plug part of the printed circuit board should be electroplated to improve the contact performance. When the circuit board is soldering, the part without tin should be masked. Use masking tape when spraying. Masking tape generally uses high strength thin paper, corrugated paper or polyester film as the base material. It also requires solvent resistance. Wave soldering masking tape requires instantaneous high temperature resistance above 230℃. Advanced nameplates and spray surfaces for household appliances, the glass screen surfaces of picture tubes, and the surfaces of electronic calculators are mostly protected by polyethylene film as the base material (a special pressure sensitive tape). Requirements are easy to peel, pressure sensitive adhesive should not remain and pollute the protection surface. Semiconductor and integrated circuit silicon wafer also need to use protective film.
Cluster fixation. The bunching and end treatment of electromagnetic coils such as deflecting coil and degaussing coil of TV are mostly made of flame-retardant PVC tape. Refrigerator, washing machine and other electrical conduit or splint fixed and sealed; Refrigerator, air conditioner production process, foamed polyurethane or foamed polyethylene and other thermal insulation material molding fixed and sealed, picture tube glass shell and the buffer between the explosion-proof hoop are used a variety of pressure sensitive tape. The plug-in automation of printed circuit board assembly requires the components to be arranged neatly. The paper based pressure sensitive tape can make a single component into a banded and orderly packaging form.
The whole machine factory then carries out the secondary sequence-coding in accordance with the pre-programmed instruction program on the basis of the various components in order, which is the only method that can carry out high-speed automatic plug-in in the electronic industry. In addition, the automatic production of porcelain capacitor, polyester capacitor and resistor also requires pressure sensitive tape for braid fixing. The trend towards miniaturization of electronic devices will increase the production of sheet (leadless) components, which will greatly increase the use of pressure-sensitive tapes and thermo-melt pressure-sensitive adhesives for the packaging of leadless components.
Double-sided paste. The installation of sound equipment scale plate, color TV door indication signs using double-sided tape can greatly improve its operability. Foamed polyurethane as the base material of double-sided tape is also widely used in audio and visual equipment for shock proof. The end reinforcement of flexible circuit boards required for miniaturization of electronic computers and other equipment, the installation of diaphragm switches used on electronic computer keyboards, and the installation and fixing of polarizing poles of liquid crystal displays all use double-sided tape.